Enhancing Maintenance Efficiency Through Work Order Software
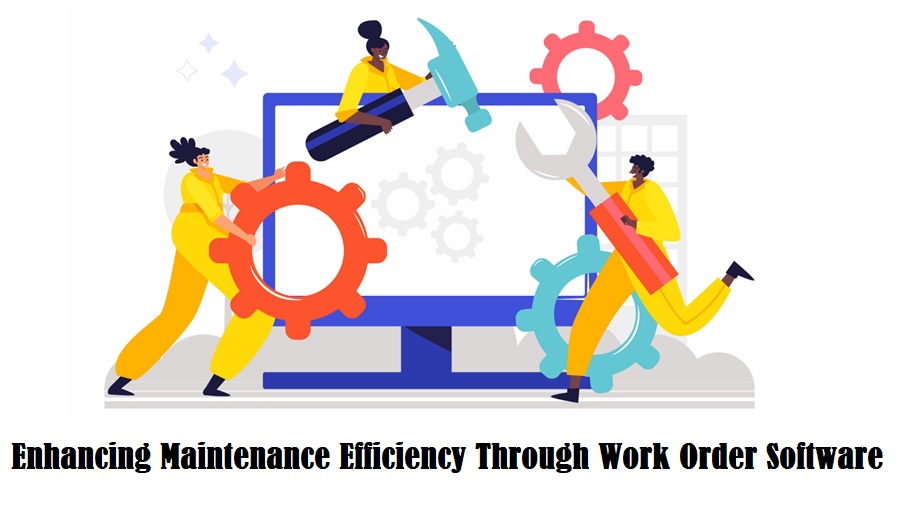
Businesses need their operations to be well-maintained, they need the least downtime, they want to curb all costs and want maximum life from their assets as well as improved safety. Still, manual processes or outdated practices typically result in inefficiencies, delays and data silos. Enter the disruptive solution of work order software, which is a digital suite for maintenance tasks management. Implementing work order software inverts workflows to encourage ease of workflow and data insights that can then be actionable for improvement of overall maintenance efficiency is one of most beneficial things you can do.
How Work Order Software Enhances Maintenance Efficiency
————————————–
Streamlining Work Order Creation and Assignment:
Digital form and predetermined templates make work request a breeze to submit, helping reduce manual data entry and error in creating formal work order.
Accurate and consistent work order creation through automated data capture will provide clear instructions the first time around while mitigating additional follow-up questions in future.
Generates the work order in a timely and precise fashion, so that maintenance can be started immediately on request and potential downtime is minimized.
Software allows us to assign work in accordance with the technical skills, status of the technician and location for data-driven resource optimization and perform the job right person.
Centralized Information and Improved Communication:
Maintenance data like asset history, manuals and checklists are all stored in the Work order software, a single central hub; where this information can be viewed by everyone who needs to know.
Automated work order progress, changes & completion notifications (providing real-time updates) for stakeholders are always kept in loops to avoid transparency and ensure less follow up in manual methods.
Facility managers, technicians and requesters can communicate via in-app messaging to answer immediate questions — simplifying inquiries and making sure the exact duties are clear.
Reducing information silos and so many errors by eliminating bottlenecks: this is what the work order software does, consolidates data and enables direct communication so that miscommunication minimizes fully lots of smoother workflows.
Efficient Scheduling and Planning:
The calendar views and drag-and-drop scheduling options offer a neatly laid out visual plan on maintenance assignment that gives technicians a better understanding of their resource allocation.
Prioritizing work orders based on urgency and impact provides the ability to quickly ensure high importance items are taken care of first, which minimizes the chances of an incident and adds to asset uptime.
Optimized overlaps and resource conflicts in technician workflows, by scheduling and planning with work order software greatly minimize overlaps thus use much lower time to complete each task overall leading to fewer delays.
Mobile Accessibility for Field Technicians:
Mobile, with current work orders — technicians can view details of the system, instructions and asset master immediately from their mobile and avoid paper-based processes or travelling to the office.
Status updates and digital forms that pop up as field technicians work across the work order, automated timesheets all provide real-time recording of progress on steps taken as well as material usage against data accuracy and lower admin overheads.
Taking photos and attaching these to the work orders gives a visual of what the problem was, the work given (or any damage) making it clear and more account responsive.
Daily Knowledge Base, Manuals & History of past work orders give techs remote access to solve onsite issues (increasing first-time fix and productivity), while all lives data synchronizing back to central system in real time.
Enhanced Tracking and Monitoring:
Work order software gives a work in progress view of all the active work orders, their status (open, in progress or complete) and technician availability and location providing instantaneous visibility over ongoing maintenance tasks.
The dashboards and reporting functionalities aggregate this real-time data into visual dashboards and written summaries of important statistics such as work order resolution times, average technician workload utilization and downtime percentage on assets for strong monitoring of maintenance operation.
This increased visibility allows for preventative detection of anything abnormal like continuous asset failures or work order processes hung to be detected rapidly and takes appropriate action for corrective, efficient improvements to the root cause to reduce disruptions
Data-Driven Insights and Reporting:
By work order software automatically capturing data of maintenance tasks-work order completion time, labor and material cost-per inventory failure rate-mechanical asset reasons for maintenance it can develop a strong data set for analysis.
With strong reporting: users can drill down and self-serve key performance indicators (KPIs) in the dashboard which makes you aware of patterns in asset performance, hot spots or trending issues and improvement areas for processes.
These data driven insights support resourceful decisions on the distribution of resources, maintenance plans and procedural optimization resulting in higher efficiency and cost saving.
Using work order software to dig into the historical maintenance data — specifically things like failure patterns and how an asset is performing — organizations can help implement planned preventive maintenance schedules to avoid these unforeseen breakdowns reducing the wear on assets.
Key Features to Look for in Work Order Software
————————————–
- Mobile Access: Mobile app is a must for field technicians Mobile: They can see work orders, change status, view asset panels and collaborate with the back office from anywhere. It eliminates the necessity of paper-based processes, saving travel time and real-time data capturing thus resulting in a fast turnaround time with high accuracy of information.
- Instant Communication: Best work order software provides a platform for almost immediate communication between everyone involved in the work order. The in-app messaging, pushing notifications for notifications and the input of notes / comments to work orders make sure that all sides are aligned. This reduces the time delays due to bringing teams on same page, speeds up issue resolution and improves collaboration on maintenance team with requestors.
- Photo Upload Capability: Directly attach photos to work order capability — context and documentation like never before system. Then it will be saved to record evidence of the issue, the work performed, or any damage found by a technician. This makes things clearer, helps with troubleshooting, establishes proof of service, and is often necessary for compliance and or to maintain as proof, thus making ambiguity and conflict of interest to reduce.
- Recurring Task Management: The software should have good support for recurring tasks, such as the most regular activities in maintenance (e.g. inspection, lubrication, filter changes etc. Software will feature a scheduling of planned preventative maintenance, never forget to do critical tasks again with this feature. Recurring work orders generated via automated order with work orders creates reduced time and promotes preventive maintenance as nothing better than avoiding costly equipment failure.
- Access to Asset Information: Immediate visibility of asset details within the work order is key for effective facility maintenance. Asset history, specifications and associated docs (egg manuals) as well as the latest service items etc. should be a click away from the work order interface so that technicians can see right away. This gives them the requisite know-how to identify the actual problem, and do the right repair, minimizing no call no ticket by reducing guesswork and increasing first time fix rate.
Conclusion:
The adoption of work order software is a giant leap for improving maintenance effectiveness in every stream of industries. Digital solutions enable the maintenance teams to work in a more precise and faster way by aligning information, workflows as well, enabling real-time communication. In the future, technology will continue to change maintenance management for the better with deeper integrated AI, IoT and predictive analytics, giving even more opportunities of preventive and optimized asset care and operating excellence.